ENGINE

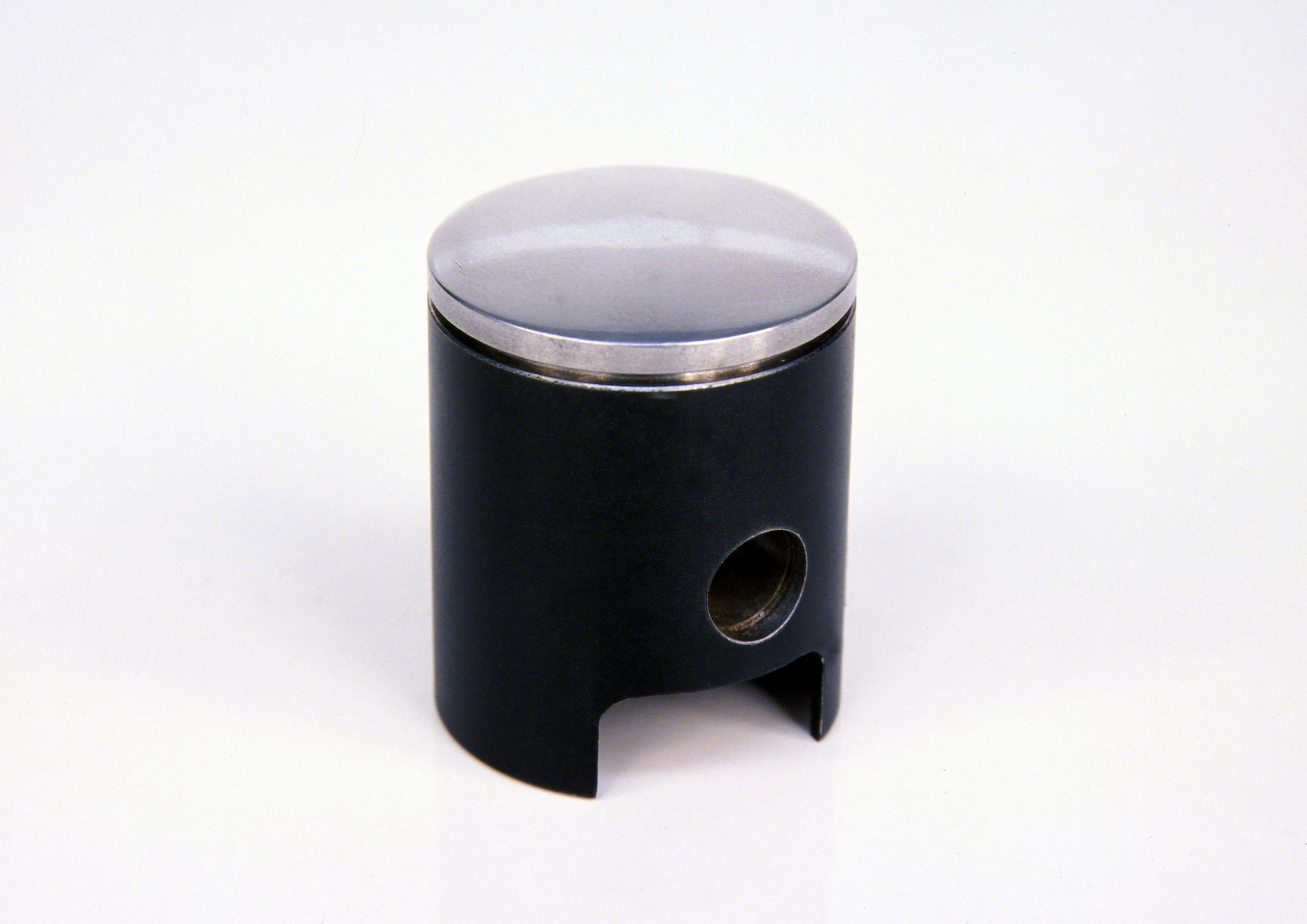
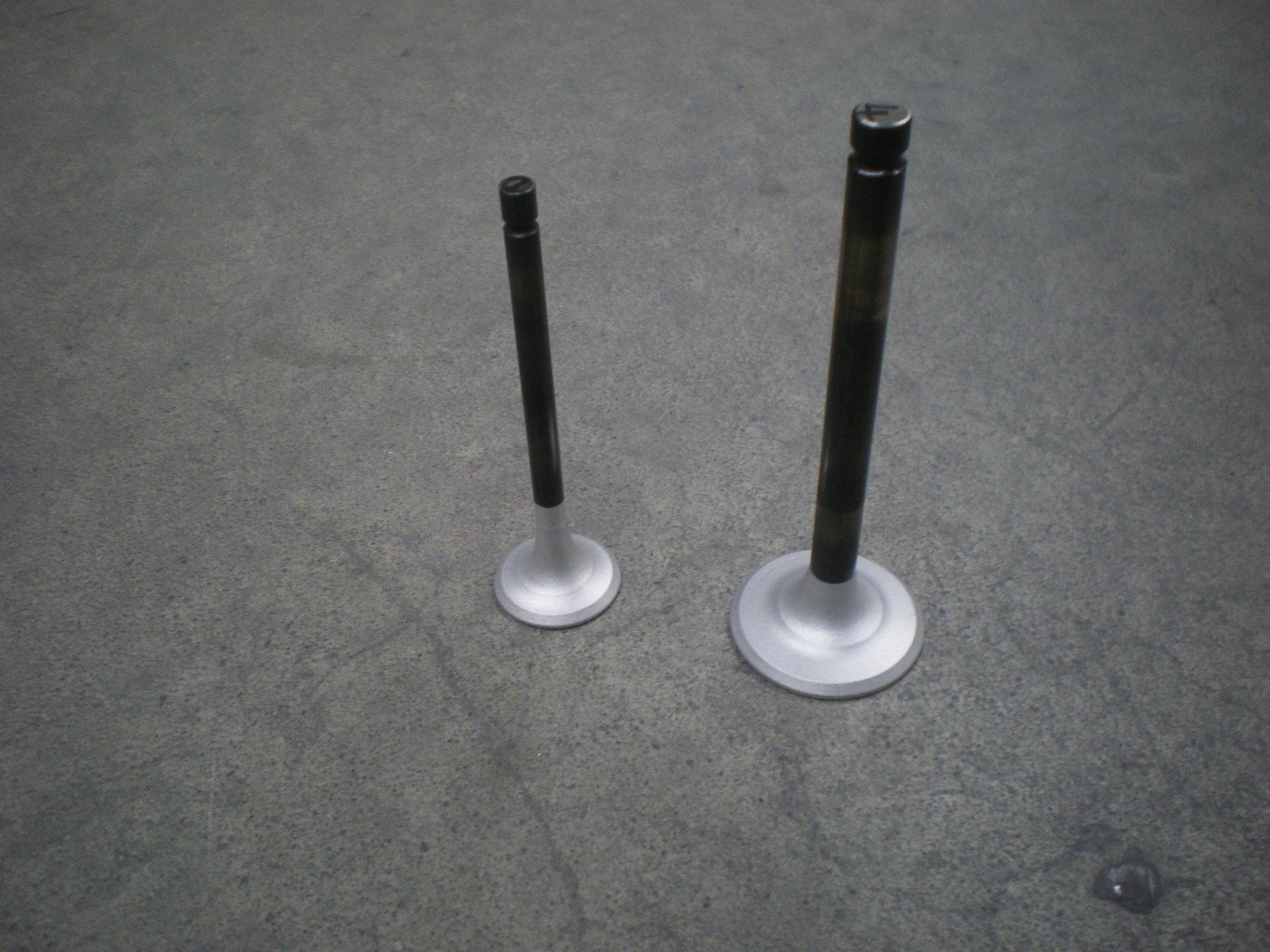
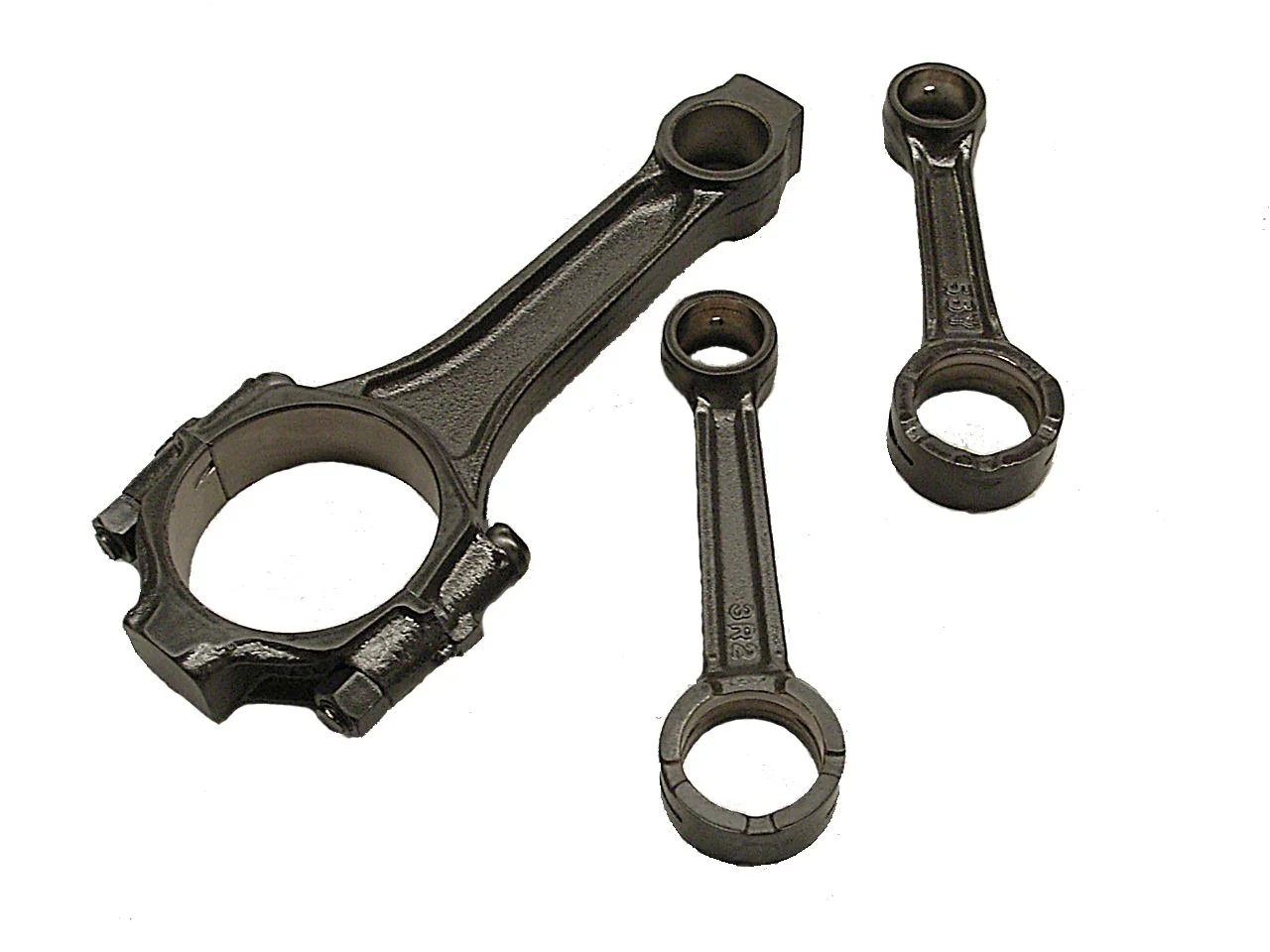
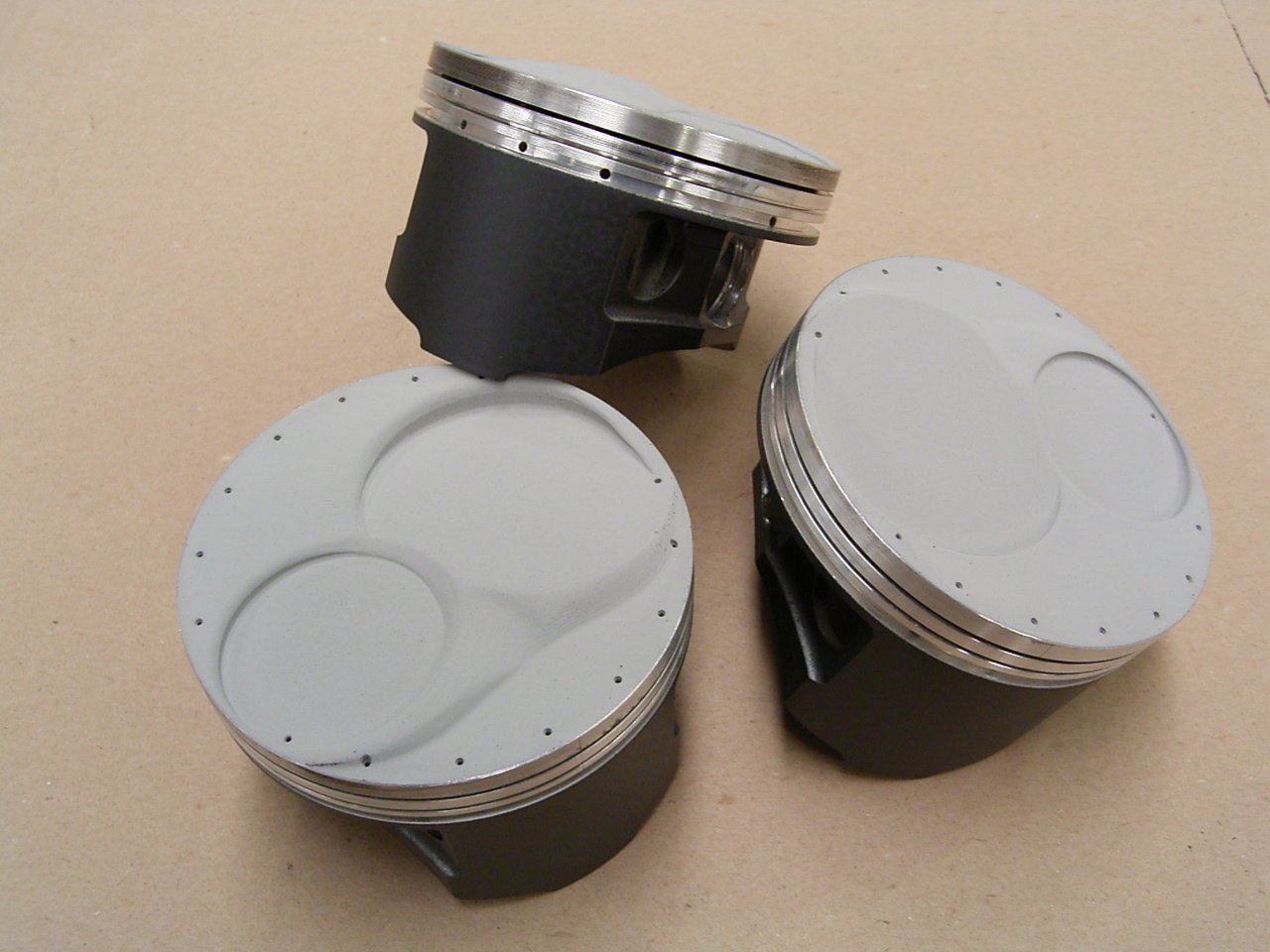
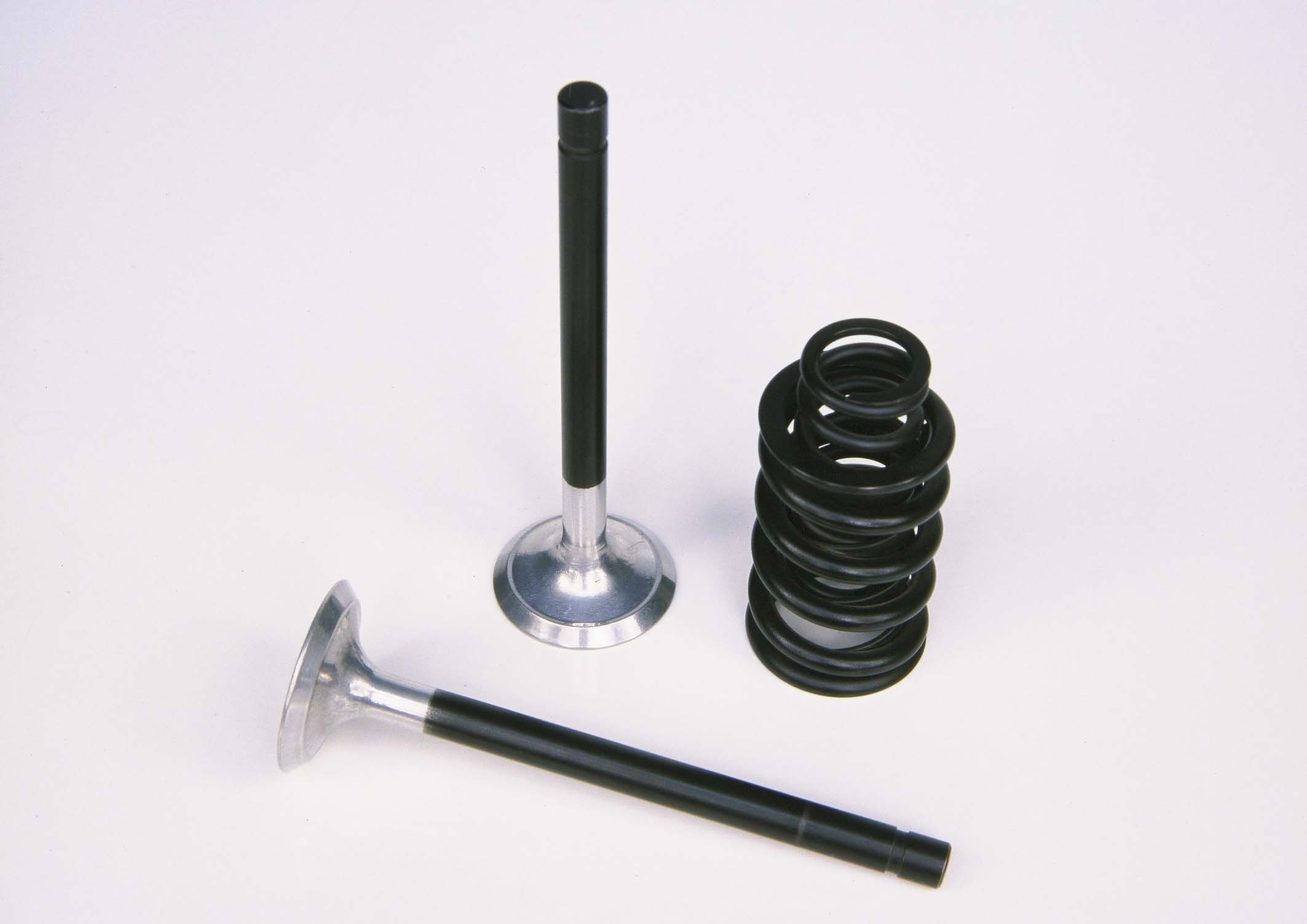

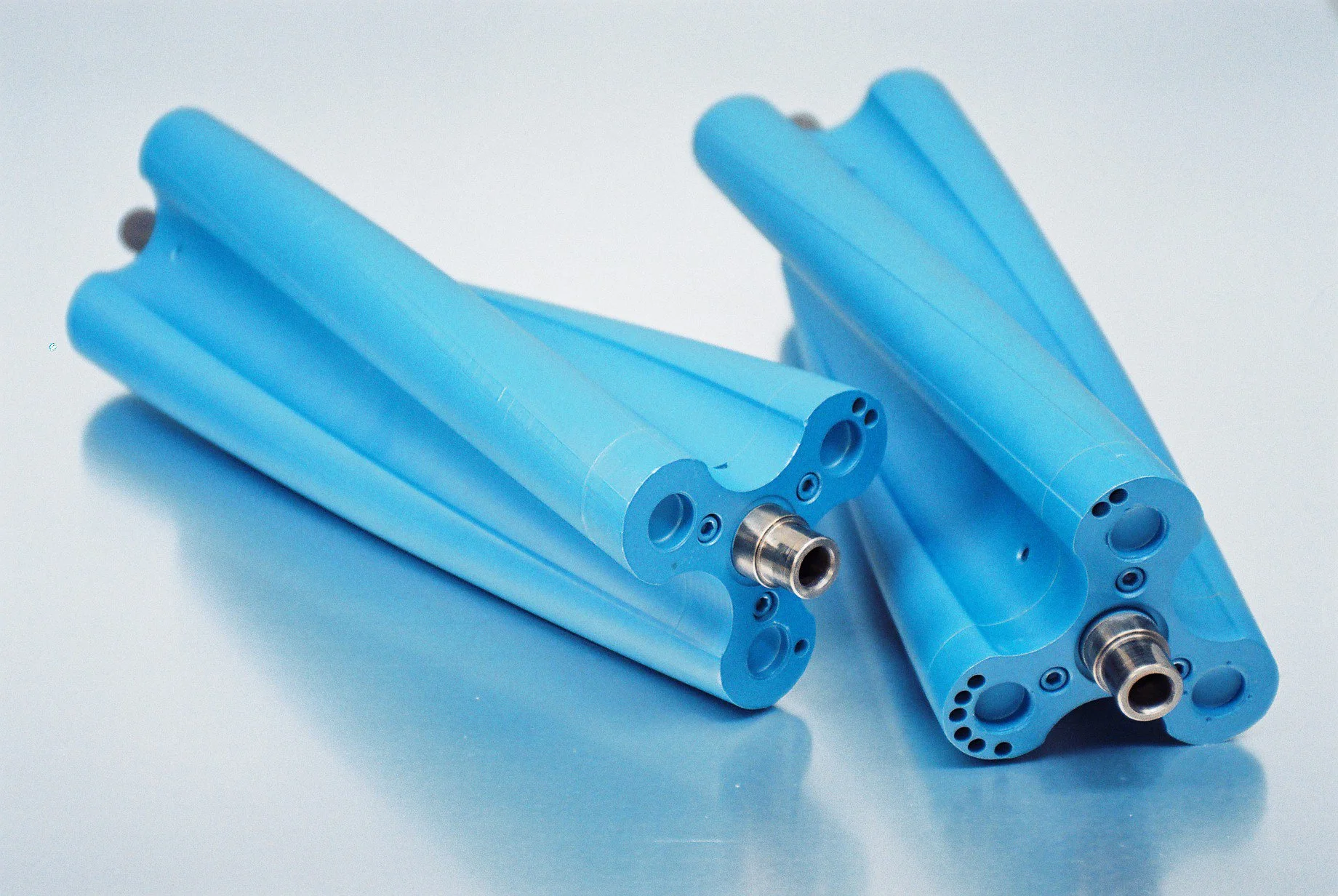
By applying HPC's Ceramic Engine Coatings to piston crowns & skirts, chambers, valves and valves springs you are helping your engine run cooler, smoother and maintain more power in the chamber where you need it most.
-
PISTONS, VALVES, COMBUSTION CHAMBERS & PORT RUNNER COATINGS ...
Combustion chambers and exhaust port runners benefit greatly from TC1, in particular, aluminium heads with a significant reduction in heat soak resulting in lower water temperature and by retaining heat in the combustion chamber fuel burn is improved.
Valves undertake extreme thermal shock. Considerable research shows that an application of TBC1 to the combustion face of the valve prevents the exhaust valve from overheating an intake tract heat transfer. The upshot is a denser air / fuel charge.
What one part suffers greater duress and thermal shock than almost every other engine part combined? The piston. That’s why we developed two distinctly different coatings to protect both the crown and skirts from wear and damage.
We apply an incredibly durable Thermal Barrier Coating (TBC1) to the combustion face of the piston, and a wettable (DF1) to the skirt. The process involves bonding particulates with an inorganic binder that is completely unaffected by petroleum products. With a bond strength of 10,000 psi, the coating’s non-porous ceramic matrix results in improved flame travel and combustion efficiency, oil temperature is reduced and it prevents carbon buildup.
HPC’s TBC1 prevents excessive heat from reaching the piston rings which results in less radial tension loss, less compression loss and less oil consumption due to the rings overheating. TBC1 prevents heat losses through the piston and cylinder temperatures are maintained. Because of this more horsepower is achieved due to increased fuel burn.
-
WETTABLE MATRIX APPLICATIONS TO PISTONS & SPRINGS ...
We also protect the piston skirts via a Molybdenum Disulfide DF1 coating designed to attract oil to ensure the piston skirt always maintains an adequate film of oil for reduced friction and scuffing.
Motorcycles, sprint cars, vintage cars, race cars, Indy cars, trucks and compressors; it really doesn’t matter what the application, a coated piston delivers improved performance.
Go-fast, low-friction engine coatings act like a sponge, soaking up oil to lubricate and reduce friction. It helps to eliminate fretting, galling and seizures and withstands fuel additives and nitromethane.
A valve spring’s biggest enemy is heat generated from compression and extension cycling, friction between the coils on double and triple springs or the spring and dampener and through absorption from the cylinder head; especially the exhaust spring being right over the exhaust port. A valve spring’s only cooling is achieved from oil splashed over it by the rocker arms.
HPC’s DF1 Solid Dry Film Lubricant coating solves the heat problems through superior high-pressure lubrication qualities and the ability to attract oil like a magnet. Valve springs coated in DF1 can retain the seat pressure up to three times longer than uncoated valve springs.
DF1 Applications ...
◦ Piston Skirts
◦ Carby Slides
◦ Springs
◦ Oil Pump Gears
-
NON-WETTABLE MATRIX APPLICATION ...
Keeping oil where it belongs is the job of our non-wettable oil-shedding DF2 coatings.
HPC’s family of non-wettable coatings is perfect in areas with little or no liquid lubricants. This process works well in eliminating exfoliation / corrosion and oxidation on zinc, aluminium and magnesium, and can be applied directly over more conventional pre-treatments such as anodising, phosphating and electroplating. The attractive satin finish sheds oil like water off a duck’s back, promoting oil return and reducing windage.
DF2 Applications ...
◦ Inside Oil Pans
◦ Windage Trays
◦ Connecting Rods
◦ Inside Valve Covers
-
HPC’s DF3 proprietary high build piston and blower rotor coating was developed for world-top fuel drag racing champion Eddy Hills blower rotors.
This inorganic single-bonded dry film contains a matrix selected to increase the lubricity and load-bearing capability when subject to high pressure and mid-range temperatures. It provides excellent wear properties while reducing friction loads.
HPC’s DF3 coating is a high-speed Teflon which reduces friction and can be built up to .003” on piston skirts or rotors.
DF3 Applications ...
◦ Piston Skirts
◦ Blower Rotors
-
DF4 Extreme release is designed with PTFE, these applications provide outstanding chemical corrosion protection on ferrous and non-ferrous materials. Dissimilar metal corrosion between tightly compressed components will be greatly reduced after being treated with DF4. Its non-wettable properties allow solutions to glide across the substrates rather than being absorbed and attacking the substrate.
DF4 Extreme release coating is ideal for plastic rotational moulds to release plastic components from the mould without using release sprays.