EXHAUST
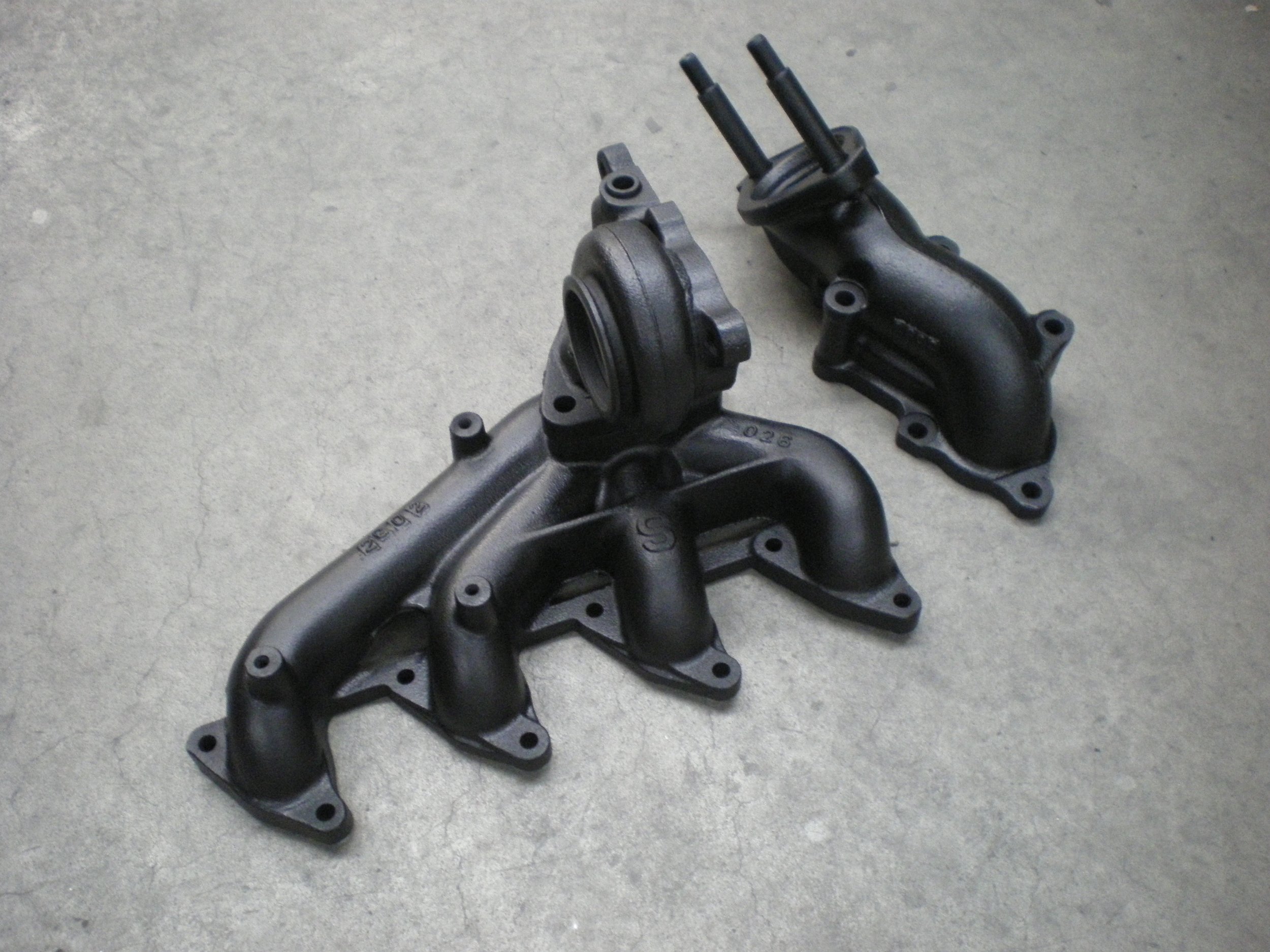
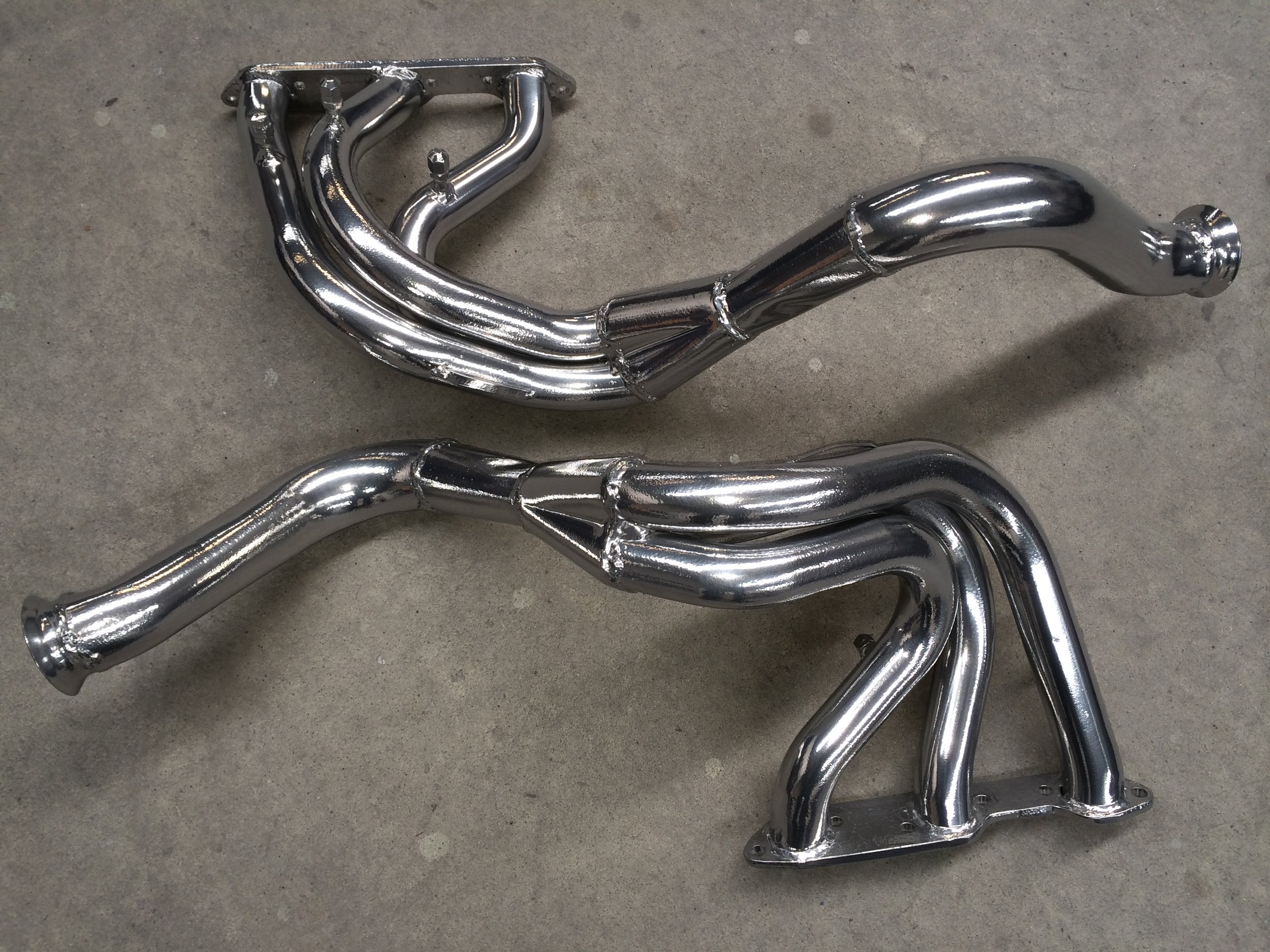
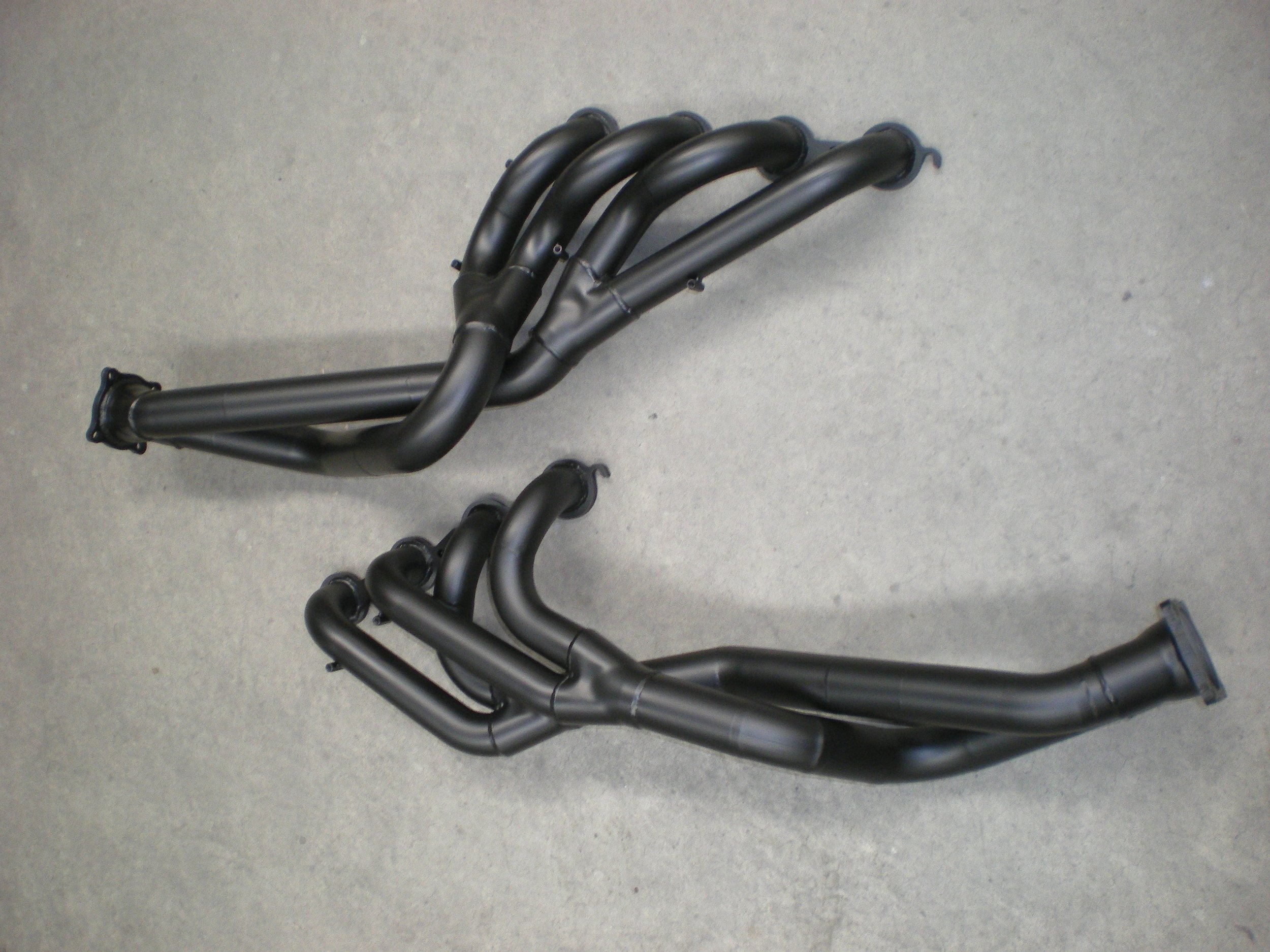
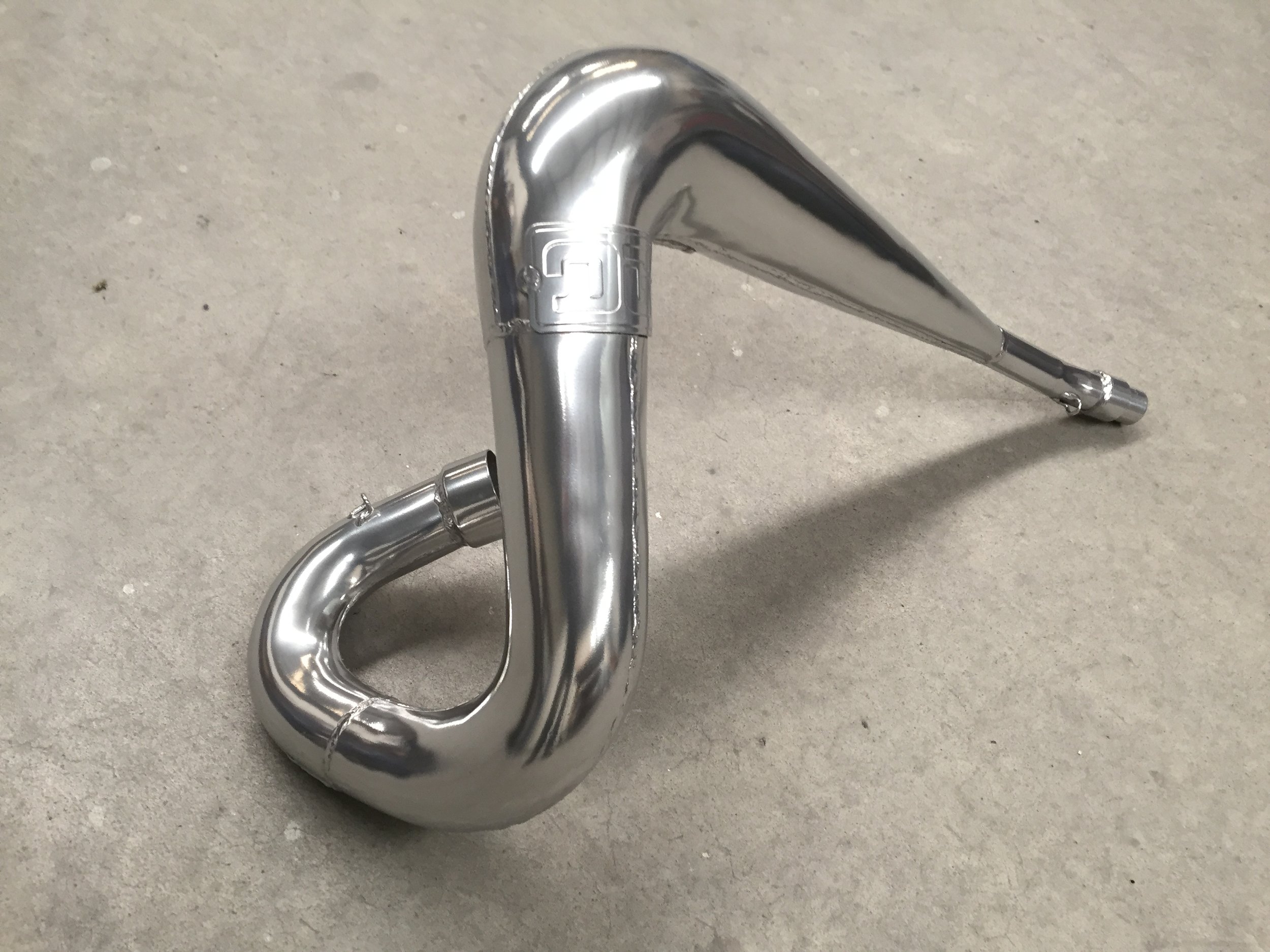
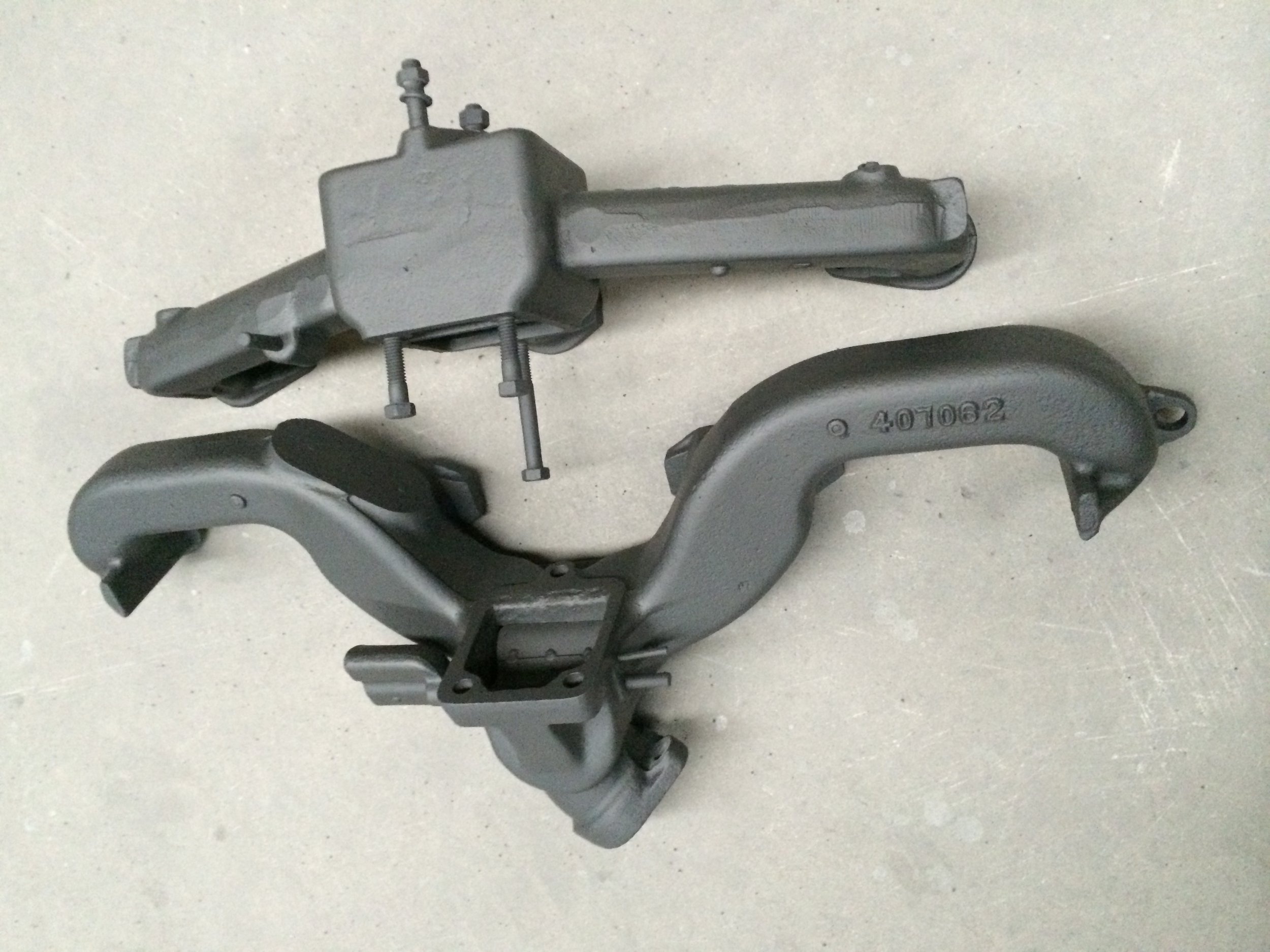


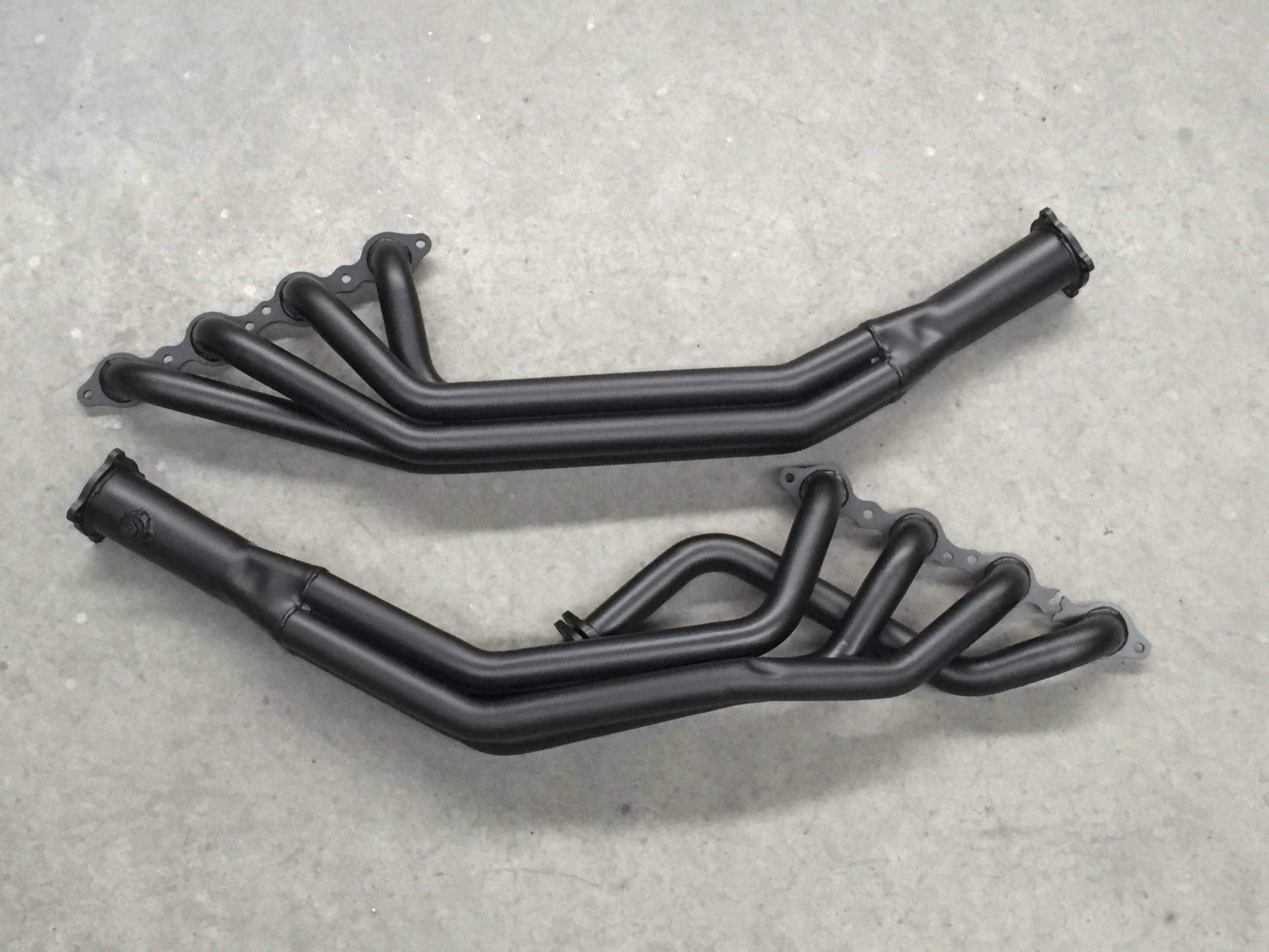
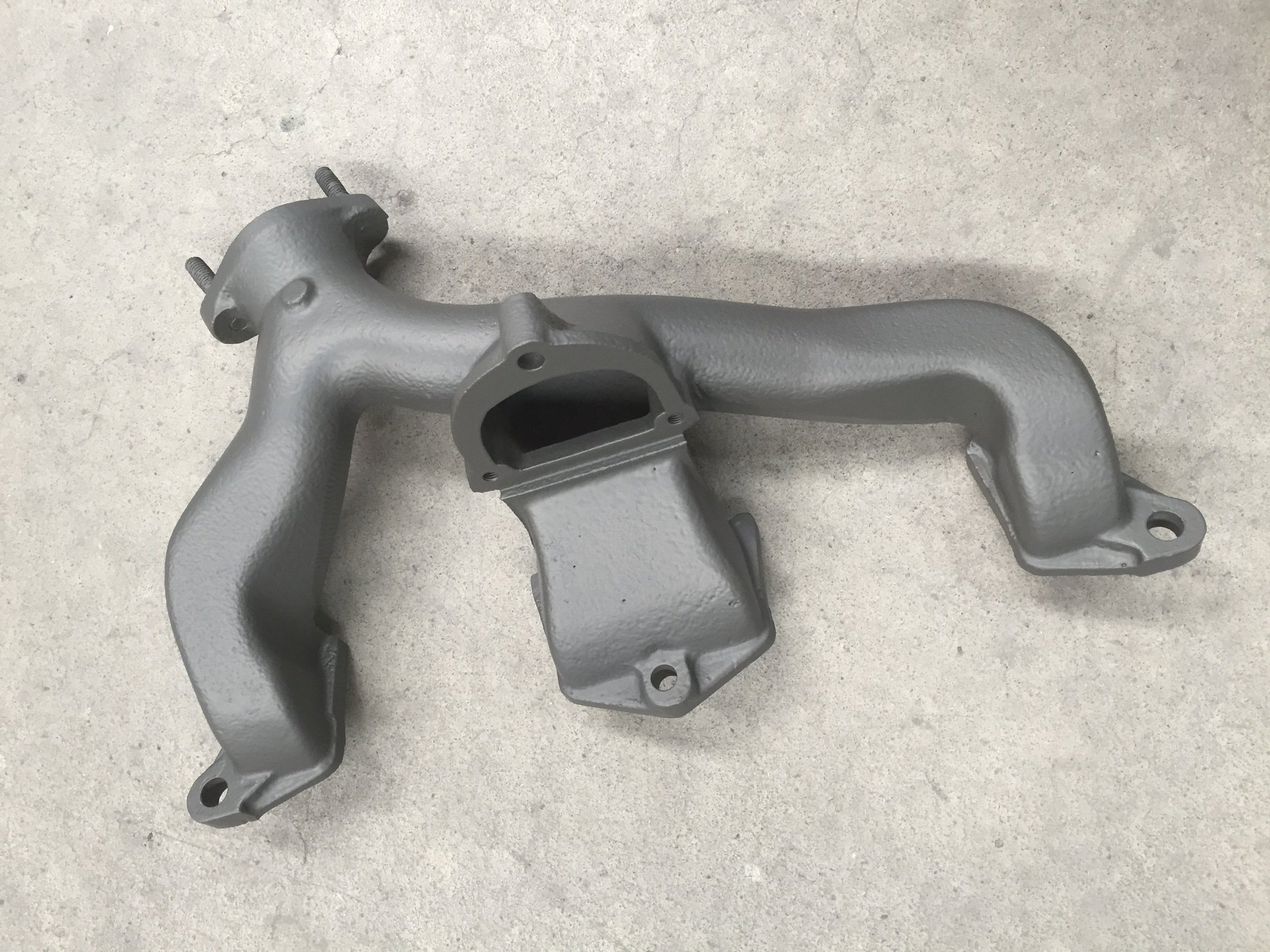
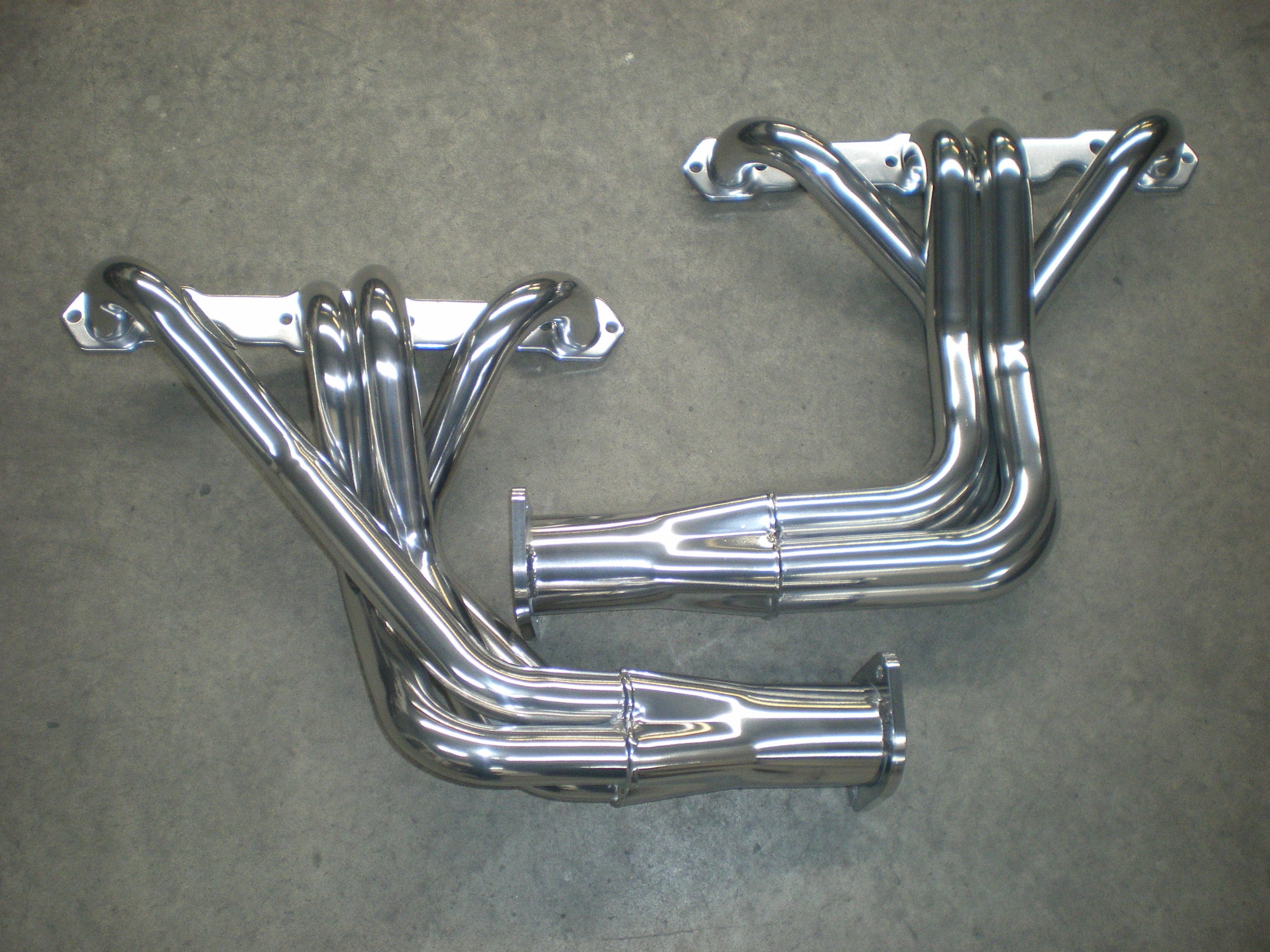
Coating your extractors, headers or manifolds with HPC's fully Australian Made Ceramic Exhaust Coatings, will not only make them look fantastic and help them last longer, the under hood heat reduction and performance gains that you will see will be significant.
-
Heavily reduced under bonnet temperatures improve engine performance and longevity, reduce fuel use and a fantastic appearance are all attributable to HPC’s HP1 exhaust coating. In recent years, HPC’s HP1 coatings have revolutionised the header / extractor industry, to the point where anyone serious about performance invariably coats their headers.
HPC’s unique HP1 process is designed to protect steel against corrosion and thermal fatigue / oxidisation created by cyclical temperatures. Performance is enhanced by reducing under-bonnet temperatures, improved air density assists combustion chamber stabilisation, and increased gas velocity is achieved by the coating’s heat retention properties.
Applied to the inside and outside of a header, HPC’s HP1 exhaust coating eliminates oxide scale, with improved laminar airflow as a direct result. Improved performance directly relates to enhanced fuel consumption, header life typically increases fivefold, while the finely polished exterior adds a lustre otherwise unobtainable in an exhaust system.
Reducing under-bonnet and undercarriage temperatures can significantly reduce heat soak in carburettors, fuel lines, master cylinders, accelerator and clutch cables as well as a myriad of other components, hence reduce component degradation for longer life and more reliable running.
These are not merely claims, rather HPC researches, manufactures and certifies its coatings to meet specific requirements. HPC’s HP1 offers protection at temperatures of -190°c to +700°c.
-
HPC’s HP2 Satin Black exhaust coating has all the benefits of HPC’s Pol Alum exhaust coating and more.
This coating is a five-coat system, with two base coats and three Nano top coats. HP2 Satin Black has proven to be highly effective in the prevention of heat scaling, oxidation, erosion / abrasion and saline corrosion. Corrosion and thermal fatigue which occur as a result of exposure to cyclical temperatures and chemical environments, can be drastically reduced.
HP2 Satin Black offers protection to your exhaust at temperatures of -170°c to +800°c so you can expect even greater heat reductions.
-
HPC’s HP3 Cast Iron Grey exhaust coating has all the benefits of HPC’s Pol Alum exhaust coating and more.
This coating is a five-coat system, with two base coats and three Nano top coats. HP3 Cast Iron Grey has proven to be highly effective in the prevention of heat scaling, oxidation, erosion / abrasion and saline corrosion. Corrosion and thermal fatigue which occur as a result of exposure to cyclical temperatures and chemical environments, can be drastically reduced.
HP3 Cast Iron Grey offers protection to your exhaust at temperatures of –170°c to +800°c, so you can expect even greater heat reduction.
-
A significant step up in its temperature handling capabilities is HPC’s TC1 coating. Specifically designed for applications such as turbochargers where substrate temperatures can exceed 1300°c. In black only, the coating helps maintain exhaust gas temperatures, increase flow velocity, aid cylinder scavenging and assist in preventing damage to hoses, belts and wiring harnesses. Indeed, it’s the experience of almost every V8 Supercar racer in the country, and race car owners in all areas of motorsport the world over, that has them coating exhaust systems.
Track testing has shown as much as a 30% reduction in under-bonnet ambient temperatures and up to a 50% reduction in component skin temperature. HPC’s TC1 achieves this by creating a thermal barrier that retains heat, which in turbo charge applications assists to increase turbo boost and spool-up. This is why today’s leading CART, NASCAR, IMSA, V8 SUPERCAR and Formula 1 Teams use HPC’s TC1 process.